Comment peut-on améliorer la maintenance d'un parc machine?
- BS Decolletage
- 1 août 2024
- 6 min de lecture
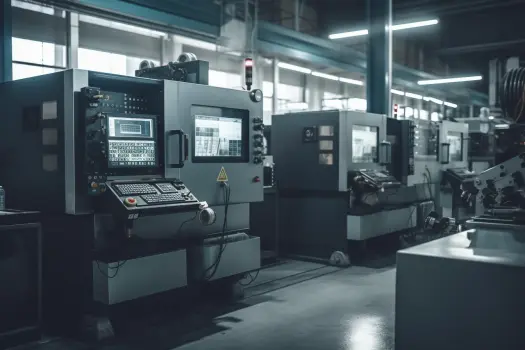
La maintenance d'un parc machine est cruciale pour garantir la continuité de la production et la longévité des équipements. Une maintenance bien planifiée et exécutée permet non seulement de réduire les pannes imprévues, mais aussi d'optimiser les performances des machines et de minimiser les coûts opérationnels. Avec les avancées technologiques et les nouvelles approches de gestion, il est désormais possible de transformer la maintenance en un atout stratégique pour l'entreprise. Cet article explore les différentes stratégies et outils pour améliorer la maintenance d'un parc machine et les avantages qu'une telle optimisation peut apporter.
Les différentes stratégies de maintenance
Une gestion efficace de la maintenance repose sur l'adoption de stratégies adaptées aux besoins et aux spécificités de chaque entreprise. Les principales stratégies incluent la maintenance préventive et la maintenance prédictive, chacune offrant des avantages distincts pour optimiser les performances des machines et réduire les coûts.
Maintenance préventive
La maintenance préventive consiste à effectuer des interventions planifiées sur les machines pour éviter les pannes imprévues et prolonger la durée de vie des équipements. Cette approche repose sur des calendriers de maintenance basés sur le temps ou l'utilisation, par exemple, en effectuant des inspections régulières, des nettoyages, des ajustements et des remplacements de pièces avant qu'elles ne se détériorent. La maintenance préventive permet de maintenir les machines en bon état de fonctionnement, de réduire les risques de défaillance et d'optimiser les performances globales. De plus, elle aide à prévoir et à contrôler les coûts de maintenance en évitant les réparations d'urgence coûteuses et les interruptions de production non planifiées.
Maintenance prédictive
La maintenance prédictive, quant à elle, utilise des technologies avancées pour anticiper les défaillances potentielles des machines avant qu'elles ne surviennent. En surveillant en continu l'état des équipements grâce à des capteurs et à l'Internet des objets (IoT), les données collectées sont analysées à l'aide de techniques de machine learning et d'algorithmes prédictifs pour identifier les signes de détérioration. Cette approche permet de planifier les interventions de maintenance de manière proactive, en fonction de l'état réel des machines plutôt que sur des intervalles de temps fixes. La maintenance prédictive offre ainsi une flexibilité accrue, une réduction des temps d'arrêt non planifiés et une optimisation des ressources en maintenance.
Technologies et outils pour une maintenance efficace
Pour améliorer la maintenance d'un parc machine, il est crucial d'intégrer des technologies et des outils modernes qui permettent une surveillance continue et une gestion optimisée des opérations de maintenance. Ces technologies facilitent la détection précoce des problèmes et la planification proactive des interventions.
Capteurs et IoT
L'utilisation de capteurs connectés et de l'Internet des objets (IoT) révolutionne la manière dont les entreprises surveillent et maintiennent leurs équipements. Les capteurs IoT peuvent être installés sur les machines pour collecter des données en temps réel sur divers paramètres tels que la température, la vibration, la pression et l'usure. Ces données sont ensuite transmises à des plateformes de gestion où elles sont analysées pour détecter des anomalies et prévoir les défaillances potentielles. Par exemple, une augmentation inhabituelle des vibrations peut indiquer un problème de roulement qui nécessite une intervention. L'IoT permet ainsi une surveillance continue et proactive, réduisant les temps d'arrêt non planifiés et optimisant l'efficacité des opérations de maintenance.
Logiciels de GMAO (Gestion de la Maintenance Assistée par Ordinateur)
Les logiciels de Gestion de la Maintenance Assistée par Ordinateur (GMAO) jouent un rôle clé dans la planification, le suivi et l'exécution des tâches de maintenance. Ces systèmes permettent de centraliser toutes les informations relatives à la maintenance, telles que les historiques de maintenance, les calendriers d'intervention, les stocks de pièces détachées et les rapports de performance. Les GMAO offrent des fonctionnalités avancées telles que la planification automatique des interventions, la gestion des ordres de travail, et la génération de rapports d'analyse pour améliorer la prise de décision. En utilisant des GMAO, les entreprises peuvent optimiser la gestion de leurs opérations de maintenance, améliorer la coordination des équipes et garantir la disponibilité des équipements.
Formation et gestion des équipes de maintenance
Pour améliorer la maintenance d'un parc machine, il est essentiel d'investir dans la formation continue des équipes et de gérer efficacement leurs compétences. Une équipe bien formée et organisée peut anticiper les problèmes, intervenir rapidement et garantir le bon fonctionnement des équipements.
Formation continue
La formation continue des équipes de maintenance est cruciale pour suivre les évolutions technologiques et les meilleures pratiques du secteur. Les technologies et les méthodes de maintenance évoluent rapidement, et il est important que les techniciens soient constamment mis à jour sur les nouvelles techniques et outils disponibles. Des programmes de formation réguliers, incluant des sessions pratiques et théoriques, permettent aux équipes de maîtriser les nouveaux équipements, de comprendre les dernières normes de sécurité et de perfectionner leurs compétences en diagnostic et réparation. En outre, la formation continue favorise la motivation et l'engagement des employés, en leur offrant des opportunités de développement professionnel et de progression de carrière.
Gestion des compétences
Une gestion efficace des compétences est essentielle pour optimiser les performances des équipes de maintenance. Cela implique de bien connaître les compétences et les qualifications de chaque membre de l'équipe, et de les affecter aux tâches les plus appropriées. Des outils de gestion des compétences peuvent aider à suivre les certifications, les formations suivies et les domaines d'expertise de chaque technicien. En répartissant les tâches en fonction des compétences spécifiques, les entreprises peuvent garantir que chaque intervention de maintenance est effectuée par le technicien le plus qualifié, ce qui réduit les risques d'erreurs et améliore l'efficacité des opérations. De plus, une gestion proactive des compétences permet de planifier les besoins futurs en formation et en recrutement, assurant ainsi que l'équipe dispose toujours des compétences nécessaires pour faire face aux défis de la maintenance.
Optimisation des processus de maintenance
L'optimisation des processus de maintenance est cruciale pour garantir une intervention rapide et efficace, minimiser les temps d'arrêt et maximiser la productivité des équipements. Cela implique la standardisation des procédures et une gestion efficace des pièces de rechange.
Standardisation des procédures
La mise en place de procédures standardisées est essentielle pour assurer une maintenance cohérente et efficace. En définissant des protocoles clairs pour chaque type d'intervention, les entreprises peuvent garantir que toutes les tâches de maintenance sont réalisées de manière uniforme et selon les meilleures pratiques. Cela inclut la documentation détaillée des étapes à suivre pour les inspections, les réparations et les remplacements de pièces, ainsi que les critères d'acceptation des travaux réalisés. La standardisation permet également de former plus facilement les nouveaux techniciens et de réduire les erreurs humaines. En outre, elle facilite l'audit et l'amélioration continue des processus de maintenance, en fournissant des bases solides pour l'analyse des performances et l'identification des domaines à améliorer.
Gestion des pièces de rechange
Une gestion efficace des pièces de rechange est cruciale pour éviter les temps d'arrêt prolongés et assurer la disponibilité des équipements. Cela implique de maintenir un inventaire optimisé des pièces critiques, d'anticiper les besoins en fonction des historiques de maintenance et des prévisions de défaillance, et de mettre en place des processus de réapprovisionnement rapides et fiables. Les systèmes de gestion des stocks automatisés peuvent aider à suivre les niveaux de stock en temps réel, à gérer les commandes et à prévenir les ruptures de stock. De plus, l'analyse des données d'utilisation des pièces peut fournir des informations précieuses pour optimiser les niveaux de stock et réduire les coûts de stockage. Une bonne gestion des pièces de rechange permet de minimiser les interruptions de production et d'assurer une maintenance réactive et efficace.
Avantages d'une maintenance optimisée
Une maintenance optimisée offre de nombreux avantages pour les entreprises, allant de la réduction des coûts à l'amélioration de la productivité et de la fiabilité des équipements.
Réduction des coûts
Une maintenance bien planifiée et exécutée permet de réduire considérablement les coûts associés aux réparations et aux remplacements d'équipements. En anticipant les problèmes potentiels grâce à des stratégies de maintenance préventive et prédictive, les entreprises peuvent éviter les pannes coûteuses et les interventions d'urgence. De plus, l'optimisation des processus de maintenance, telle que la gestion efficace des pièces de rechange et la standardisation des procédures, permet de réduire les coûts opérationnels en minimisant les temps d'arrêt et en maximisant l'efficacité des ressources. Une réduction des coûts de maintenance se traduit directement par une meilleure rentabilité pour l'entreprise.
Amélioration de la productivité
Une maintenance optimisée contribue à améliorer la productivité globale de l'entreprise en garantissant la disponibilité et la performance optimale des équipements. En minimisant les interruptions de production et en assurant un fonctionnement continu des machines, les entreprises peuvent maintenir des niveaux élevés de production et répondre efficacement aux demandes des clients. De plus, la maintenance proactive permet de prolonger la durée de vie des équipements, réduisant ainsi la nécessité d'investir dans de nouveaux équipements coûteux. En maintenant un parc machine en bon état de fonctionnement, les entreprises peuvent également améliorer la qualité des produits et réduire les taux de défauts, ce qui renforce la satisfaction des clients et la réputation de l'entreprise.
Améliorer la maintenance d'un parc machine est essentiel pour garantir la continuité et l'efficacité des opérations industrielles. En ad
optant des stratégies de maintenance préventive et prédictive, en utilisant des technologies avancées comme les capteurs IoT et les logiciels de GMAO, et en investissant dans la formation continue et la gestion des compétences des équipes, les entreprises peuvent optimiser leurs processus de maintenance. Une maintenance bien planifiée et exécutée permet non seulement de réduire les coûts de réparation et de remplacement, mais aussi d'améliorer la productivité et la fiabilité des équipements. En intégrant ces pratiques, les entreprises peuvent transformer la maintenance en un avantage concurrentiel majeur et assurer leur succès à long terme.
Article rédigé par la technologie Open AI L'erreur est humaine ? L'IA peut en faire aussi ! Si vous remarquez une erreur ou une faute, n'hésitez pas à prendre contact avec nous pour que nous la rectifions !
Comments